Product code: N/A
enterasy A4H254-8F8T
¥66,666.00 Original price was: ¥66,666.00.¥1,450.00Current price is: ¥1,450.00.
If you have any products that you cannot find, you can consult anytime.
🌍Country of origin: USA France Germany Estonia Norway UK
⌚Delivery date: in stock
🛠After-sales service: brand new with one year warranty
⚙️ Product Category: Module/Controller/Server/Motor/Touch Screen
🕰Warranty: 12 months/365 days
☎️ Please contact me: 15359029662 Ms. Amy Sun
📎Chinese official website: www.dcsplcabb.com
📩Email: geabbamy@gmail.com
💬Whatsapp: +86 15359029662
Detailed content
Product details:
Product No. :enterasy A4H254-8F8T
Delivery time: Available in stock
Estimated Lead Time: 1-2 weeks
Factory warranty: 12 months
Datasheet manual : Download here
Color code : White/Blue/Green/Black
Ships to : Worldwide
Dimension : 250mm*220mm*40mm
Operation mode: Direct on-board/Need test
Product situation: Discontinued
Shipping weight: 2.3kg
Website: www.fy-module.com
Contact me :+8615359029662 Whatsapp/Wechat
Email: geabbamy@gmail.com
Call me: Amy
DCS, PLC, SCADA are common control systems in the field of industrial automation. The following introduces and compares them from the aspects of operation, technical parameters, hardware specifications, etc.:
DCS (Distributed Control System)
Operation usage
Control strategy: Suitable for continuous reaction process control, such as power generation, chemical, pharmaceutical and other industries. It can implement complex control strategies such as cascade control, ratio control, feedforward feedback control, etc., and can accurately adjust multiple parameters in the production process.
Monitoring management: With a user-friendly human-machine interface, operators can centrally monitor and manage the entire production process in the central control room. It can display production data, equipment status and other information in real time, and can perform operations such as alarm management, historical data query and report generation.
Maintenance management: Supports online maintenance and fault diagnosis, allowing real-time monitoring of various modules in the system, timely detection and handling of faults, and reducing downtime.
DCS (Distributed Control System)
Operation usage
Control strategy: Suitable for continuous reaction process control, such as power generation, chemical, pharmaceutical and other industries. It can implement complex control strategies such as cascade control, ratio control, feedforward feedback control, etc., and can accurately adjust multiple parameters in the production process.
Monitoring management: With a user-friendly human-machine interface, operators can centrally monitor and manage the entire production process in the central control room. It can display production data, equipment status and other information in real time, and can perform operations such as alarm management, historical data query and report generation.
Maintenance management: Supports online maintenance and fault diagnosis, allowing real-time monitoring of various modules in the system, timely detection and handling of faults, and reducing downtime.
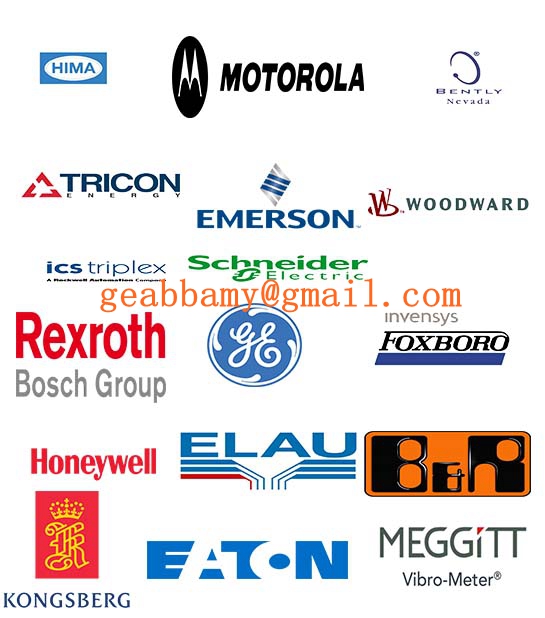
Technical Parameter
Control accuracy: It can usually achieve high control accuracy, for example, in temperature control, the accuracy can be controlled within ± 0.1 ℃, meeting the production process with high requirements for product quality.
Scanning cycle: The scanning cycle is relatively short, usually ranging from tens to hundreds of milliseconds, and can quickly respond to changes in the production process.
System capacity: It can support a large number of input and output points, ranging from a few hundred to tens of thousands, suitable for large and complex industrial production processes.
Hardware specifications
Controller: Generally uses high-performance processors with powerful computing and data processing capabilities. Having multiple communication interfaces, it can perform high-speed data transmission with other devices.
Input/output modules: There are various types, including analog input/output modules, digital input/output modules, etc., which can be flexibly configured according to different production needs.
Operation station: equipped with high-performance computers and displays, with a good human-computer interaction interface, convenient for operators to operate and monitor.
PLC (Programmable Logic Controller)
Operation usage
Logic control: mainly used in discrete manufacturing processes, such as automotive assembly lines, packaging machinery, etc. It can achieve various logical control functions, such as sequential control, timing control, counting control, etc.
Flexible programming: Using programming languages such as ladder diagrams and instruction lists, programming is simple and easy to understand, and can be flexibly programmed according to different production processes.
Easy to expand: The system structure is flexible and can easily increase or decrease input and output modules according to production needs, achieving system expansion and upgrading.
Control accuracy: It can usually achieve high control accuracy, for example, in temperature control, the accuracy can be controlled within ± 0.1 ℃, meeting the production process with high requirements for product quality.
Scanning cycle: The scanning cycle is relatively short, usually ranging from tens to hundreds of milliseconds, and can quickly respond to changes in the production process.
System capacity: It can support a large number of input and output points, ranging from a few hundred to tens of thousands, suitable for large and complex industrial production processes.
Hardware specifications
Controller: Generally uses high-performance processors with powerful computing and data processing capabilities. Having multiple communication interfaces, it can perform high-speed data transmission with other devices.
Input/output modules: There are various types, including analog input/output modules, digital input/output modules, etc., which can be flexibly configured according to different production needs.
Operation station: equipped with high-performance computers and displays, with a good human-computer interaction interface, convenient for operators to operate and monitor.
PLC (Programmable Logic Controller)
Operation usage
Logic control: mainly used in discrete manufacturing processes, such as automotive assembly lines, packaging machinery, etc. It can achieve various logical control functions, such as sequential control, timing control, counting control, etc.
Flexible programming: Using programming languages such as ladder diagrams and instruction lists, programming is simple and easy to understand, and can be flexibly programmed according to different production processes.
Easy to expand: The system structure is flexible and can easily increase or decrease input and output modules according to production needs, achieving system expansion and upgrading.